Keyhole Plasma welding of 10mm plates
Arcraft Plasma Equipments(I) Pvt Ltd has for the first time in India developed a plasma welding system for single pass keyhole welding of 10mm thick SS plates. Extensive trials have been undertaken and the welded plates radiographically tested to ASME SEC.IX 191.2 , the results have been without significant defects and accepted as passed by the testing authority.
Micrograph of welded sample at Arcraft showing dendritritic structure.
The system consists of
Inverter Power Supply
Plasma Console
Water re-circulator
Plasma Welding Torch
Torch Accessory Kit (Tips, ceramics, collets, electrodes set-up gages)
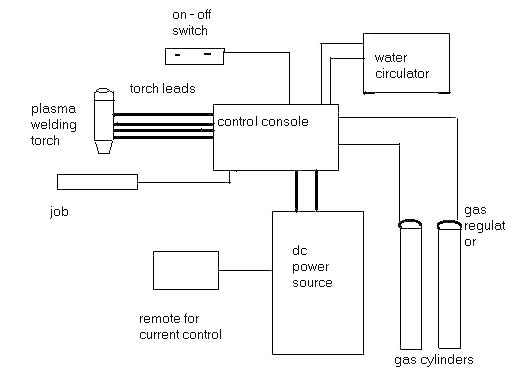
Typical layout of plasma welding system
Plasma welding derives its unique operating characteristics from the torch design. As in TIG welding, the arc is formed between the end of a small diameter tungsten electrode and the workpiece . However, in the plasma torch, the electrode is positioned behind a fine bore copper nozzle. Plasma is present in all arcs. If a constricting orifice is placed around the arc, the amount of ionization , or plasma , is increased. This results in a higher arc temperature and a more concentrated heat pattern than exists in TIG welding.The higher temperature forms the weld pool much faster and uses 50 to 60 % less current as compared to the TIG welding process. Plasma welding used in this way is often referred to as the Melt in mode of operation.
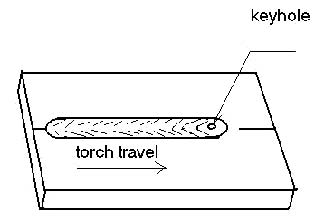
Keyhole plasma is carried out by increasing the current level and the plasma gas flow. This generates a very powerful arc plasma, similar to a laser beam. During welding, the plasma arc slices through the metal producing a keyhole, with the molten metal flowing around the keyhole to form the weld. Full penetration and high welding speeds can be achieved with this operating mode.
As the plasma arc is generated by the special torch arrangement and system controller, the equipment can be obtained as an add-on unit to conventional TIG equipment after providing additional pilot arc and separate plasma and shielding gases. Alternatively, purpose-built plasma equipment is available for critical applications.
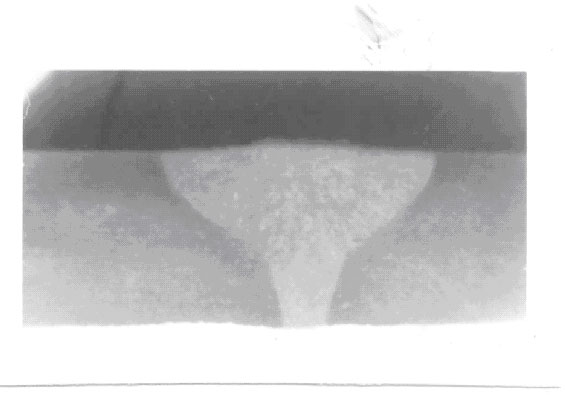
Photo of plasma weld of 10mm SS plate completed at Arcraft showing a wine glass crossection.
Cost of welding / welding speed of 10 mm plate using keyhole plasmaPlasma gas Ar Flow = 0.01 m³/min
Sheilding gas Ar + H² = .02 m³/min
Welding speed = 250mm /min or 1mtr/4 min
Plasma gas Ar Flow for welding 1 mtr = 0.04 m³/min
Sheilding gas Ar + H² for welding 1 mtr = .08 m³/min
Cost of Ar /mtr = Rs 700x0.04 m³
___ = Rs 4.00 7 m³
Cost of Ar+H² /mtr= Rs 1600x0.08 m³
___ = 14.16
9 m³
Power Cost v3 VA = KVA
-------- = KW /hr- PF1.73 x 415 x 23 ------ = 18348 Watts 0.9KW x unit cost = cost per hour
18.34x5.5 = Rs 101/ hr
101 x 4 = Rs 6.73 / mtr----60Total cost of gas and power = Rs 25 per mtrWelding speed = 1 mtr / 4 min
Benefits of single pass plasma welding of 10 mm plate as compared to TIG welding
No edge preparation required reducing joint preparation and machining costs .
Filler wire is not required reducing costs .
Greater joint penetration eliminates back chipping or multiple pass welding reducing costs of gas , electricity and labour .
Multiple torches not required.
Heat content is higher , less current and higher welding speeds as compared to TIG.
Concentrated energy density reduces heat affected zone, improves weld quality and reduces distortion.
The symmetrical fusion zone of the keyhole weld reduces the tendency for transverse distortion.
The plasma gas flushing through the open keyhole helps remove gases that would under other circumstances be trapped as porosity in molten metal.
Reasonable variations in torch standoff distance has little effect on bead width or heat concentration at the work, this makes out of position welding much easier in the melt in mode.
Protected electrode, offers long times before electrode maintenance and eliminates tungsten contamination.
Stable arc during arc starting and welding produces consistent results.
HF only initiates pilot arc start, not for each weld .There is only minimal high frequency noise used in plasma arc welding to start the pilot arc, thus plasma can be more easily used with NC controls with less fear of the arc starting noise causing problems in any electrical equipment.Metals welded
Plasma arc welding is used to join most of the metals commonly welded by GTAW. These metals include carbon and low alloy steels, stainless steels, copper alloys, nickel and cobalt based alloys, Titanium alloys.
Welding Positions
Keyhole welding is generally done in the flat position using automatic movement for the torch which was also adopted at Arcraft for the trials.
Manual PAW generally is considered to be an all position process using the melt in mode. Mechanized PAW is done in the flat and horizontal positions. Arcraft has designed torches suitable for both manual and mechanized operations.
Applications
Modern Plasma equipment and welding techniques have improved to where these processes can address applications which were formerly catered to by more expensive processes such as laser or electron beam welding. Precision plasma arc welding systems are now the optimum solution. This has helped to reduce or eliminate the formerly high capital costs, running costs and service costs associated with the manufacturing processes using laser and electron beam.
In many applications, many of the unique advantages of plasma combine to benefit the overall welding process. Plasma arc welding is adaptable to both manual and mechanized operation , and can be used to produce either continuous or intermittent welds. The plasma process is equally suited to manual and automatic
applications. It has been used in a variety of operations ranging from single pass full penetration welds on space shuttle fuel tanks , hulls for hydrofoil boats and submarines , tanks used in chemical , Food and dairy processing , pharmaceutical industry , high volume welding of strip metal, tube mills , automatic repair of jet engine blades and many more. The installation of plasma welding system in tube mills can increase the speed of the tube mill by more than 100%, particularly in thick walled tubes and can make possible the manufacture of 6 to 12.5 mm thick tubes in tube mills which is otherwise very difficult by TIG welding.
Arcraft plasma has with dedicated research and development developed the whole range of plasma welding equipment capable of welding upto 10mm thick plates for the present with further increase in future . |