CHARACTERISTICS
7-1. GENERAL
Most of the metals and alloys used in Army materiel can be welded by one or more of the processes described in this manual. This section describes the characteristics of metals and their alloys, with particular reference to their significance in welding operations.
7-2. PROPERTIES OF METALS
a. Definitions. All metals fall within two categories, ferrous or nonferrous.
(1) Ferrous metals are metals that contain iron. Ferrous metals appear in the form of cast iron, carbon steel, and tool steel. The various alloys of iron, after undergoing certain processes, are pig iron, gray cast iron, white iron, white cast iron, malleable cast iron, wrought iron, alloy steel, and carbon steel. All these types of iron are mixtures of iron and carbon, manganese, sulfur, silicon, and phosphorous. Other elements are also present, but in amounts that do not appreciably affect the characteristics of the metal.
(2) Nonferrous metals are those which do not contain iron. Aluminum, copper, magnesium, and titanium alloys are among those metals which belong to this group.
b. Physical Properties. Many of the physical properties of metals determine if and how they can be welded and how they will perform in service. Physical properties of various metals are shown in table 7-1.
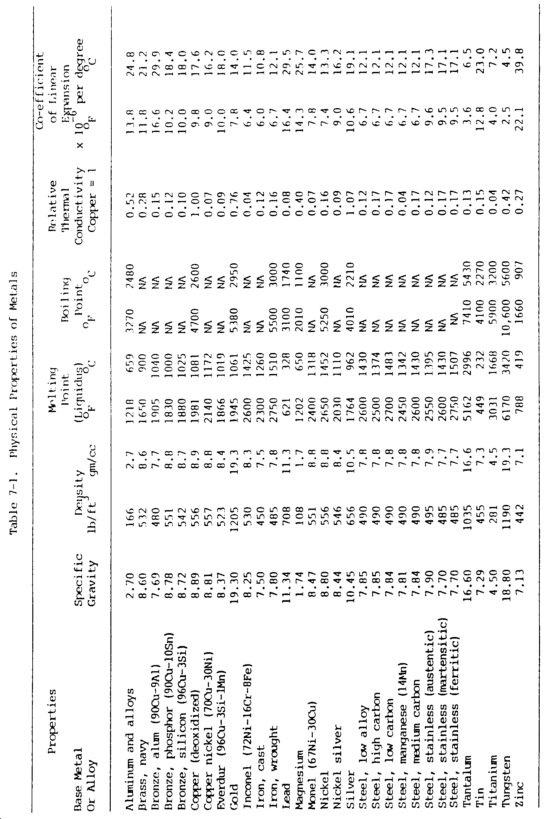
(1) Color. Color relates to the quality of light reflected from the metal.
(2) Mass or density. Mass or density relates to mass with respect to volume. Commonly known as specific gravity, this property is the ratio of the mass of a given volume of the metal to the mass of the same volume of water at a specified temperature, usually 39°F (4°C). For example, the ratio of weight of one cubic foot of water to one cubic foot of cast iron is the specific gravity of cast iron. This property is measured by grams per cubic millimeter or centimeter in the metric system.
(3) Melting point. The melting point of a metal is important with regard to welding. A metal's fusibility is related to its melting point, the temperature at which the metal changes from a solid to a molten state. Pure substances have a sharp melting point and pass from a solid state to a liquid without a change in temperature. During this process, however, there is an absorption of heat during melting and a liberation of heat during freezing. The absorption or release of thermal energy when a substance changes state is called its latent heat. Mercury is the only common metal that is in its molten state at normal room temperature. Metals having low melting temperatures can be welded with lower temperature heat sources. The soldering and brazing processes utilize low-temperature metals to join metals having higher melting temperatures.
(4) Boiling point. Boiling point is also an important factor in welding. The boiling point is the temperature at which the metal changes from the liquid state to the vapor state. Some metals, when exposed to the heat of an arc, will vaporize.
(5) Conductivity. Thermal and electrical conductivity relate to the metal's ability to conduct or transfer heat and electricity. Thermal conductivity, the ability of a metal to transmit heat throughout its mass, is of vital importance in welding, since one metal may transmit heat from the welding area much more quickly than another. The thermal conductivity of a metal indicates the need for preheating and the size of heat source required. Thermal conductivity is usually related to copper. Copper has the highest thermal conductivity of the common metals, exceeded only by silver. Aluminum has approximately half the thermal conductivity of copper, and steels have abut one-tenth the conductivity of copper. Thermal conductivity is measured in calories per square centimeter per second per degree Celsius. Electrical conductivity is the capacity of metal to conduct an electric current. A measure of electrical conductivity is provided by the ability of a metal to conduct the passage of electrical current. Its opposite is resistivity, which is measured in micro-ohms per cubic centimeter at a standardize temperature, usually 20°C. Electrical conductivity is usually considered as a percentage and is related to copper or silver. Temperature bears an important part in this property. As temperature of a metal increases, its conductivity decreases. This property is particularly important to resistance welding and to electrical circuits.
(6) Coefficient of linear thermal expansion. With few exceptions, solids expand when they are heated and contract when they are cooled. The coefficient of linear thermal expansion is a measure of the linear increase per unit length based on the change in temperature of the metal. Expansion is the increase in the dimension of a metal caused by heat. The expansion of a metal in a longitudinal direction is known as the linear expansion. The coefficient of linear expansion is expressed as the linear expansion per unit length for one degree of temperature increase. When metals increase in size, they increase not only in length but also in breadth and thickness. This is called volumetric expansion. The coefficient of linear and volumetric expansion varies over a wide range for different metals. Aluminum has the greatest coefficient of expansion, expanding almost twice as much as steel for the same temperature change. This is important for welding with respect to warpage, wapage control and fixturing, and for welding together dissimilar metals.
(7) Corrosion resistance. Corrosion resistance is the resistance to eating or wearing away by air, moisture, or other agents.
c. Mechanical Properties. The mechanical properties of metals determine the range of usefulness of the metal and establish the service that can be expected. Mechanical properties are also used to help specify and identify the metals. They are important in welding because the weld must provide the same mechanical properties as the base metals being joined. The adequacy of a weld depends on whether or not it provides properties equal to or exceeding those of the metals being joined. The most common mechanical properties considered are strength, hardness, ductility, and impact resistance. Mechanical properties of various metals are shown in table 7-2.
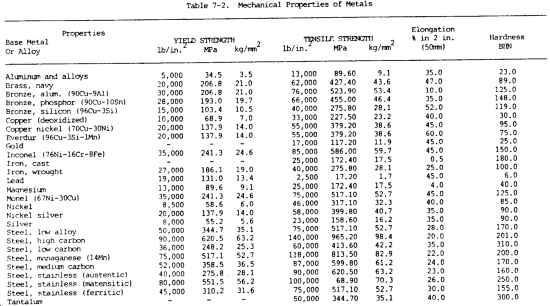
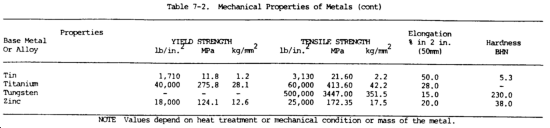
(1) Tensile strength. Tensile strength is defined as the maximum load in tension a material will withstand before fracturing, or the ability of a material to resist being pulled apart by opposing forces. Also known as ultimate strength, it is the maximum strength developed in a metal in a tension test. (The tension test is a method for determining the behavior of a metal under an actual stretch loading. This test provides the elastic limit, elongation, yield point, yield strength, tensile strength, and the reduction in area.) The tensile strength is the value most commonly given for the strength of a material and is given in pounds per square inch (psi) (kiloPascals (kPa)). The tensile strength is the number of pounds of force required to pull apart a bar of material 1.0 in. (25.4 mm) wide and 1.00 in. (25.4 mm) thick (fig. 7-1).
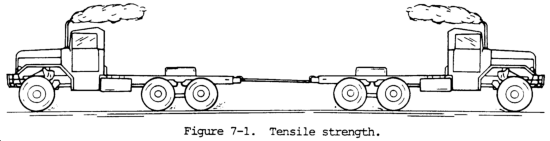
(2) Shear strength. Shear strength is the ability of a material to resist being fractured by opposing forces acting of a straight line but not in the same plane, or the ability of a metal to resist being fractured by opposing forces not acting in a straight line (fig. 7-2).
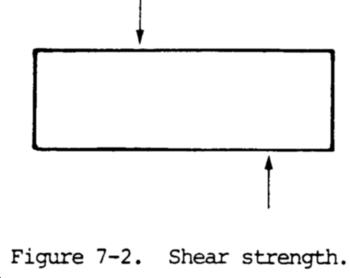
(3) Fatigue strength. Fatigue strength is the maximum load a material can withstand without failure during a large number of reversals of load. For example, a rotating shaft which supports a weight has tensile forces on the top portion of the shaft and compressive forces on the bottom. As the shaft is rotated, there is a repeated cyclic change in tensile and compressive strength. Fatigue strength values are used in the design of aircraft wings and other structures subject to rapidly fluctuating loads. Fatigue strength is influenced by microstructure, surface condition, corrosive environment, and cold work.
(4) Compressive strength. Compressive strength is the maximum load in compression a material will withstand before a predetermined amount of deformation, or the ability of a material to withstand pressures acting in a given plane (fig. 7-3). The compressive strength of both cast iron and concrete are greater than their tensile strength. For most materials, the reverse is true.
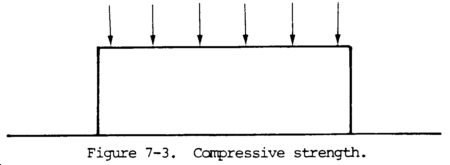
(5) Elasticity. Elasticity is the ability of metal to return to its original size, shape, and dimensions after being deformed, stretched, or pulled out of shape. The elastic limit is the point at which permanent damage starts. The yield point is the point at which definite damage occurs with little or no increase in load. The yield strength is the number of pounds per square inch (kiloPascals) it takes to produce damage or deformation to the yield point.
(6) Modulus of elasticity. The modulus of elasticity is the ratio of the internal stress to the strain produced.
(7) Ductility. The ductility of a metal is that property which allows it to be stretched or otherwise changed in shape without breaking, and to retain the changed shape after the load has been removed. It is the ability of a material, such as copper, to be drawn or stretched permanently without fracture. The ductility of a metal can be determined by the tensile test by determining the percentage of elongation. The lack of ductility is brittleness or the lack of showing any permanent damage before the metal cracks or breaks (such as with cast iron).
(8) Plasticity. Plasticity is the ability of a metal to be deformed extensively without rupture. Plasticity is similar to ductility.
(9) Malleability. Malleability is another form of plasticity, and is the ability of a material to deform permanently under compression without rupture. It is this property which allows the hammering and rolling of metals into thin sheets. Gold, silver, tin, and lead are examples of metals exhibiting high malleability. Gold has exceptional malleability and can be rolled into sheets thin enough to transmit light.
(10) Reduction of area. This is a measure of ductility and is obtained from the tensile test by measuring the original cross-sectional area of a specimen to a cross-sectional area after failure.
(11) Brittleness. Brittleness is the property opposite of plasticity or ductility. A brittle metal is one than cannot be visibly deformed permanently, or one that lacks plasticity.
(12) Toughness. Toughness is a combination of high strength and medium ductility. It is the ability of a material or metal to resist fracture, plus the ability to resist failure after the damage has begun. A tough metal, such as cold chisel, is one that can withstand considerable stress, slowly or suddenly applied, and which will deform before failure. Toughness is the ability of a material to resist the start of permanent distortion plus the ability to resist shock or absorb energy.
(13) Machinability and weldability. The property of machinability and weldability is the ease or difficulty with which a material can be machined or welded.
(14) Abrasion resistance. Abrasion resistance is the resistance to wearing by friction.
(15) Impact resistance. Resistance of a metal to impacts is evaluated in terms of impact strength. A metal may possess satisfactory ductility under static loads, but may fail under dynamic loads or impact. The impact strength of a metal is determined by measuring the energy absorbed in the fracture.
(16) Hardness. Hardness is the ability of a metal to resist penetration and wear by another metal or material. It takes a combination of hardness and toughness to withstand heavy pounding. The hardness of a metal limits the ease with which it can be machined, since toughness decreases as hardness increases. Table 7-3 illustrates hardness of various metals.
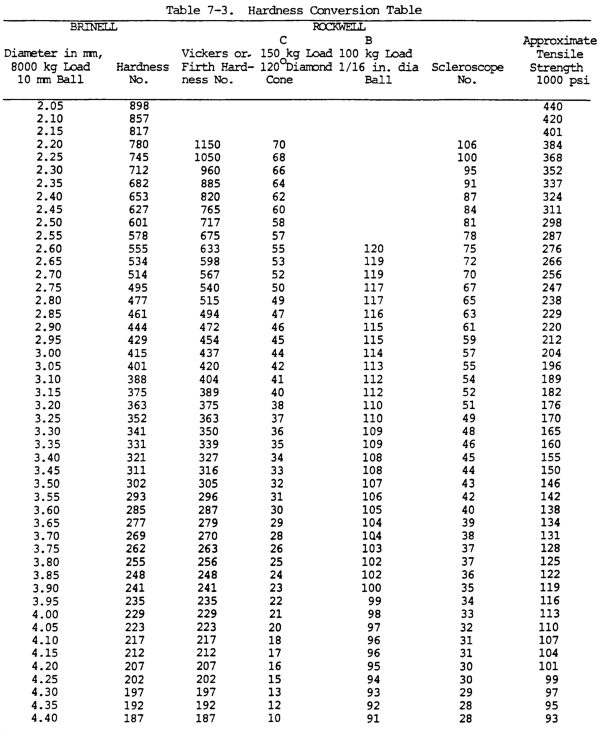
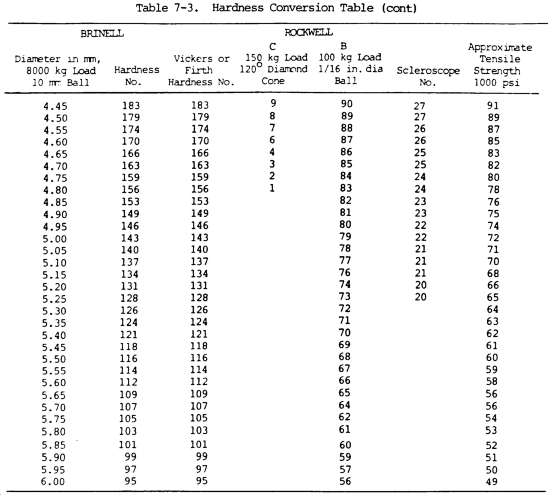
(a) Brinell hardness test. In this test, a hardened steel ball is pressed slowly by a known force against the surface of the metal to be tested. The diameter of the dent in the surface is then measured, and the Brinell hardness number (bhn) is determined by from standard tables (table 7-3).
(b) Rockwell hardness test. This test is based upon the difference between the depth to which a test point is driven into a metal by a light load and the depth to which it is driven in by a heavy load. The light load is first applied and then, without moving the piece, the heavy load is applied. The hardness number is automatically indicated on a dial. The letter designations on the Rockwell scale, such as B and C, indicate the type of penetrator used and the amount of heavy load (table 7-3). The same light load is always used.
(c) Scleroscope hardness test. This test measures hardness by letting a diamond-tipped hammer fall by its own weight from a fixed height and rebound from the surface; the rebound is measured on a scale. It is used on smooth surfaces where dents are not desired.
a. General. It is necessary to know the composition of the metal being welded in order to produce a successful weld. Welders and metal workers must be able to identify various metal products so that proper work methods may be applied. For Army equipment, drawings (MWOs) should be available. They must be examined in order to determine the metal to be used and its heat treatment, if required. After some practice, the welder will learn that certain parts of machines or equipment are always cast iron, other parts are usually forgings, and so on.
b. Tests. There are seven tests that can be performed in the shop to identify metals. Six of the different tests are summarized in table 7-4. These should be supplemented by tables 7-1 and 7-2 which present physical and mechanical properties of metal, and table 7-3, which presents hardness data. These tests are as follows:

(1) Appearance test. The appearance test includes such things as color and appearance of machined as well as unmachined surfaces. Form and shape give definite clues as to the identity of the metal. The shape can be descriptive; for example, shape includes such things as cast engine blocks, automobile bumpers, reinforcing rods, I beams or angle irons, pipes, and pipe fittings. Form should be considered and may show how the part was rode, such as a casting with its obvious surface appearance and parting mold lines, or hot rolled wrought material, extruded or cold rolled with a smooth surface. For example, pipe can be cast, in which case it would be cast iron, or wrought, which would normally be steel. Color provides a very strong clue in metal identification. It can distinguish many metals such as copper, brass, aluminum, magnesium, and the precious metals. If metals are oxidized, the oxidation can be scraped off to determine the color of the unoxidized metal. This helps to identify lead, magnesium, and even copper. The oxidation on steel, or rust, is usually a clue that can be used to separate plain carbon steels from the corrosion-resisting steels.
(2) Fracture test. Some metal can be quickly identified by looking at the surface of the broken part or by studying the chips produced with a hammer and chisel. The surface will show the color of the base metal without oxidation. This will be true of copper, lead, and magnesium. In other cases, the coarseness or roughness of the broken surface is an indication of its structure. The ease of breaking the part is also an indication of its ductility of lack of ductility. If the piece bends easily without breaking, it is one of the more ductile metals. If it breaks easily with little or no bending, it is one of the brittle metals.
(3) Spark test. The spark test is a method of classifying steels and iron according to their composition by observing the sparks formed when the metal is held against a high speed grinding wheel. This test does not replace chemical analysis, but is a very convenient and fast method of sorting mixed steels whose spark characteristics are known. When held lightly against a grinding wheel, the different kinds of iron and steel produce sparks that vary in length, shape, and color. The grinding wheel should be run to give a surface speed of at least 5000 ft (1525 m) per minute to get a good spark stream. Grinding wheels should be hard enough to wear for a reasonable length of time, yet soft enough to keep a free-cutting edge. Spark testing should be done in subdued light, since the color of the spark is important. In all cases, it is best to use standard samples of metal for the purpose of comparing their sparks with that of the test sample.
(a) Spark testing is not of much use on nonferrous metals such as coppers, aluminums, and nickel-base alloys, since they do not exhibit spark streams of any significance. However, this is one way to separate ferrous and nonferrous metals.
(b) The spark resulting from the test should be directed downward and studied. The color, shape, length, and activity of the sparks relate to characteristics of the material being tested. The spark stream has specific items which can be identified. The straight lines are called carrier lines. They are usually solid and continuous. At the end of the carrier line, they may divide into three short lines, or forks. If the spark stream divides into more lines at the end, it is called a sprig. Sprigs also occur at different places along the carrier line. These are called either star or fan bursts. In some cases, the carrier line will enlarge slightly for a very short length, continue, and perhaps enlarge again for a short length. When these heavier portions occur at the end of the carrier line, they are called spear points or buds. High sulfur creates these thicker spots in carrier lines and the spearheads. Cast irons have extremely short streams, whereas low-carbon steels and most alloy steels have relatively long streams. Steels usually have white to yellow color sparks, while cast irons are reddish to straw yellow. A 0.15 percent carbon steel shows sparks in long streaks with some tendency to burst with a sparkler effect; a carbon tool steel exhibits pronounced bursting; and a steel with 1.00 percent carbon shows brilliant and minute explosions or sparklers. As the carbon content increases, the intensity of bursting increases.
(c) One big advantage of this test is that it can be applied to metal in, all stages, bar stock in racks, machined forgings or finished parts. The spark test is best conducted by holding the steel stationary and touching a high speed portable grinder to the specimen with sufficient pressure to throw a horizontal spark stream about 12.00 in. (30.48 cm) long and at right angles to the line of vision. Wheel pressure against the work is important because increasing pressure will raise the temperature of the spark stream and give the appearance of higher carbon content. The sparks near and around the wheel, the middle of the spark stream, and the reaction of incandescent particles at the end of the spark stream should be observed. Sparks produced by various metals are shown in figure 7-4.

CAUTION
The torch test should be used with discretion, as it may damage the part being tested. Additionally, magnesium may ignite when heated in the open atmosphere.
(4) Torch test. With the oxyacetylene torch, the welder can identify various metals by studying how fast the metal melts and how the puddle of molten metal and slag looks, as well as color changes during heating. When a sharp corner of a white metal part is heated, the rate of melting can be an indication of its identity. If the material is aluminum, it will not melt until sufficient heat has been used because its high conductivity. If the part is zinc, the sharp corner will melt quickly, since zinc is not a good conductor. In the case of copper, if the sharp comer melts, it is normally deoxidized copper. If it does not melt until much heat has been applied, it is electrolytic copper. Copper alloys, if composed of lead, will boil. To distinguish aluminum from magnesium, apply the torch to filings. Magnesium will burn with a sparkling white flame. Steel will show characteristic colors before melting.
(5) Magnetic test. The magnetic test can be quickly performed using a small pocket magnet. With experience, it is possible to judge a strongly magnetic material from a slightly magnetic material. The nonmagnetic materials are easily recognized. Strongly magnetic materials include the carbon and low-alloy steels, iron alloys, pure nickel, and martensitic stainless steels. A slightly magnetic reaction is obtained from Monel and high-nickel alloys and the stainless steel of the 18 chrome 8 nickel type when cold worked, such as in a seamless tube. Nonmagnetic materials include copper-base alloys, aluminum-base alloys, zinc-base alloys, annealed 18 chrome 8 nickel stainless, the magnesium, and the precious metals.
(6) Chisel test. The chip test or chisel test may also be used to identify metals. The only tools required are a banner and a cold chisel. Use the cold chisel to hammer on the edge or corner of the material being examined. The ease of producing a chip is an indication of the hardness of the metal. If the chip is continuous, it is indicative of a ductile metal, whereas if chips break apart, it indicates a brittle material. On such materials as aluminum, mild steel and malleable iron, the chips are continuous. They are easily chipped and the chips do not tend to break apart. The chips for gray cast iron are so brittle that they become small, broken fragments. On high-carbon steel, the chips are hard to obtain because of the hardness of the material, but can be continuous.
(7) Hardness test. Refer to table 7-3 for hardness values of the various metals, and to the above information on the three hardness tests that are commonly used. A less precise hardness test is the file test. A summary of the reaction to filing, the approximate Brinell hardness, and the possible type of steel is shown in table 7-6. A sharp mill file must be used. It is assumed that the part is steel and the file test will help identify the type of steel.
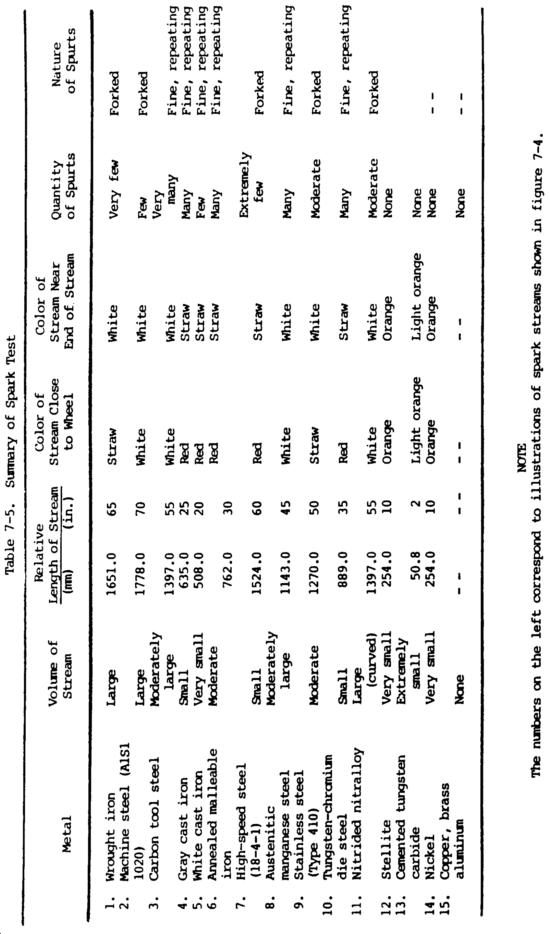
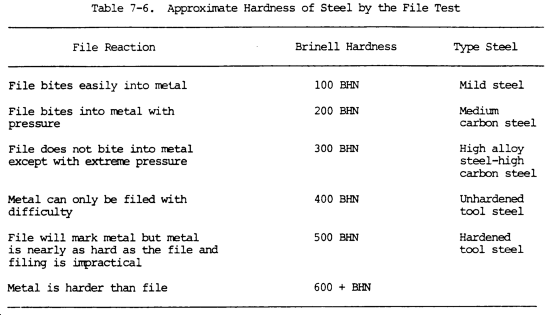
(8) Chemical test. There are numerous chemical tests than can be made in the shop to identify some material. Monel can be distinguished form Inconel by one drop of nitric acid applied to the surface. It will turn blue-green on Monel, but will show no reaction on Inconel. A few drops of a 45 percent phosphoric acid will bubble on low-chromium stainless steels. Magnesium can be distinguished from aluminum using silver nitrate, which will leave a black deposit on magnesium, but not on aluminum. These tests can become complicated, and for this reason are not detailed further here.
c. Color Code for Marking Steel Bars. The Bureau of Standards of the United States Department of Commerce has a color code for making steel bars. The color markings provided in the code may be applied by painting the ends of bars. Solid colors usually mean carbon steel, while twin colors designate alloy and free-cutting steel.
d. Ferrous Metal. The basic substance used to make both steel and cast iron (gray and malleable) is iron. It is used in the form of pig iron. Iron is produced from iron ore that occurs chiefly in nature as an oxide, the two most important oxides being hematite and magnetite. Iron ore is reduced to pig iron in a blast furnace, and the impurities are removed in the form of slag (fig. 7-5). Raw materials charged into the furnace include iron ore, coke, and limestone. The pig iron produced is used to manufacture steel or cast iron.
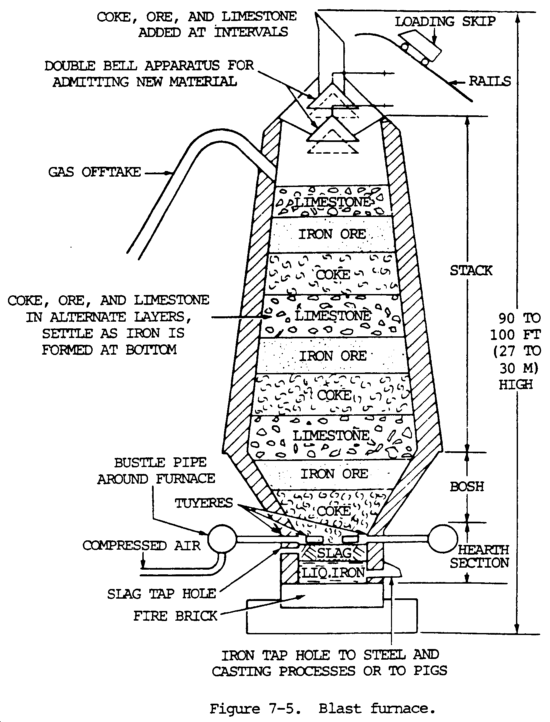
Plain carbon steel consists of iron and carbon. Carbon is the hardening element. Tougher alloy steel contains other elements such as chromium, nickel, and molybdenum. Cast iron is nothing more than basic carbon steel with more carbon added, along with silicon. The carbon content range for steel is 0.03 to 1.7 percent, and 4.5 percent for cast iron.
Steel is produced in a variety of melting furnaces, such as open-hearth, Bessemer converter, crucible, electric-arc, and induction. Most carbon steel is made in open-hearth furnaces, while alloy steel is melted in electric-arc and induction furnaces. Raw materials charged into the furnace include mixtures of iron ore, pig iron, limestone, and scrap. After melting has been completed, the steel is tapped from the furnace into a ladle and then poured into ingots or patterned molds. The ingots are used to make large rectangular bars, which are reduced further by rolling operations. The molds are used for castings of any design.
Cast iron is produced by melting a charge of pig iron, limestone, and coke in a cupola furnace. It is then poured into sand or alloy steel molds. When making gray cast iron castings, the molten metal in the mold is allowed to become solid and cool to room temperature in open air. Malleable cast iron, on the other hand, is made from white cast iron, which is similar in content to gray cast iron except that malleable iron contains less carbon and silicon. White cast iron is annealed for more than 150 hours at temperatures ranging from 1500 to 1700°F (815 to 927°C). The result is a product called malleable cast iron. The desirable properties of cast iron are less than those of carbon steel because of the difference in chemical makeup and structure. The carbon present in hardened steel is in solid solution, while cast iron contains free carbon known as graphite. In gray cast iron, the graphite is in flake form, while in malleable cast iron the graphite is in nodular (rounded) form. This also accounts for the higher mechanical properties of malleable cast iron as compared with gray cast iron.
Iron ore is smelted with coke and limestone in a blast furnace to remove the oxygen (the process of reduction) and earth foreign matter from it. Limestone is used to combined with the earth matter to form a liquid slag. Coke is used to supply the carbon needed for the reduction and carburization of the ore. The iron ore, limestone, and coke are charged into the top of the furnace. Rapid combustion with a blast of preheated air into the smelter causes a chemical reaction, during which the oxygen is removed from the iron. The iron melts, and the molten slag consisting of limestone flux and ash from the coke, together with compounds formed by reaction of the flux with substances present in the ore, floats on the heavier iron liquid. Each material is then drawn off separately (fig. 7-6).
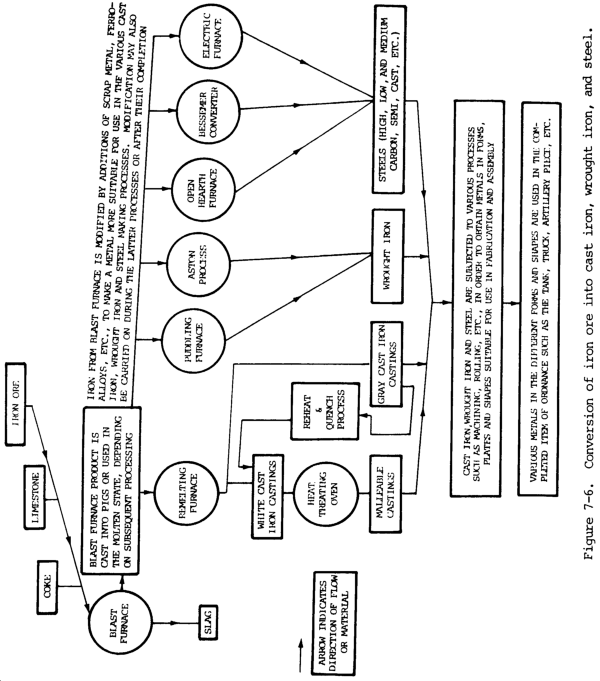
All forms of cast iron, steel, and wrought iron consist of a mixture of iron, carbon, and other elements in small amounts. Whether the metal is cast iron or steel depends entirely upon the amount of carbon in it. Table 7-7 shows this principle.
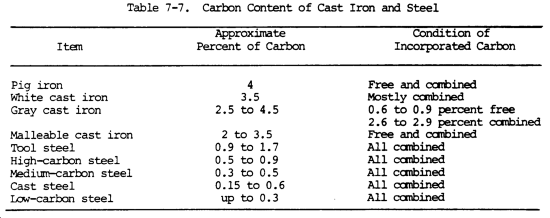
Cast iron differs from steel mainly because its excess of carbon (more than 1.7 percent) is distributed throughout as flakes of graphite, causing most of the remaining carbon to separate. These particles of graphite form the paths through which failures occur, and are the reason why cast iron is brittle. By carefully controlling the silicon content and the rate of cooling, it is possible to cause any definite amount of the carbon to separate as graphite or to remain combined. Thus, white, gray, and malleable cast iron are all produced from a similar base.
(1) Wrought iron.
(a) General. Wrought iron is almost pure iron. It is made from pig iron in a puddling furnace and has a carbon content of less than 0.08 percent. Carbon and other elements present in pig iron are taken out, leaving almost pure iron. In the process of manufacture, some slag is mixed with iron to form a fibrous structure in which long stringers of slag, running lengthwise, are mixed with long threads of iron. Because of the presence of slag, wrought iron resists corrosion and oxidation, which cause rusting.
(b) Uses. Wrought iron is used for porch railings, fencing, farm implements, nails, barbed wire, chains, modern household furniture, and decorations.
(c) Capabilities. Wrought iron can be gas and arc welded, machined,plated, and is easily formed.
(d) Limitations. Wrought iron has low hardness and low fatigue strength.
(e) Properties. Wrought iron has Brinell hardness number of 105; tensile strength of 35,000 psi; specific gravity of 7.7; melting point of 2750°F (1510°C); and is ductile and corrosion resistant.
(f) Appearance test. The appearance of wrought iron is the same as that of rolled, low-carbon steel.
(g) Fracture test. Wrought iron has a fibrous structure due to threads of slag. As a result, it can be split in the direction in which the fibers run. The metal is soft and easily cut with a chisel, and is quite ductile. When nicked and bent, it acts like rolled steel. However, the break is very jagged due to its fibrous structure. Wrought iron cannot be hardened.
(h) Spark test. When wrought iron is ground, straw-colored sparks form near the grinding wheel, and change to white, forked sparklers near the end of the stream.
(i) Torch test. Wrought iron melts quietly without sparking. It has a peculiar slag coating with white lines that are oily or greasy in appearance.
(2) Cast iron (gray, white, and malleable).
(a) General. Cast iron is a manmade alloy of iron, carbon, and silicon. A portion of the carbon exists as free carbon or graphite. Total carbon content is between 1.7 and 4.5 percent.
(b) Uses. Cast iron is used for water pipes, machine tool castings, transmission housing, engine blocks, pistons, stove castings, etc.
(c) Capabilities. Cast iron may be brazed or bronze welded, gas and arc welded, hardened, or machined.
(d) Limitations. Cast iron must be preheated prior to welding. It cannot be worked cold.
(e) Properties. Cast iron has a Brinell hardness number of 150 to 220 (no alloys) and 300 to 600 (alloyed); tensile strength of 25,000 to 50,000 psi (172,375 to 344,750 kPa) (no alloys) and 50,000 to 100,000 psi (344,750 to 689,500 kPa) (alloyed); specific gravity of 7.6; high compressive strength that is four times its tensile strength; high rigidity; good wear resistance; and fair corrosion resistance.
(f) Gray cast iron. If the molten pig iron is permitted to cool slowly, the chemical compound of iron and carbon breaks up to a certain extent. Much of the carbon separates as tiny flakes of graphite scattered throughout the metal. This graphite-like carbon, as distinguish from combined carbon, causes the gray appearance of the fracture, which characterizes ordinary gray cast iron. Since graphite is an excellent lubricant, and the metal is shot throughout with tiny, flaky cleavages, gray cast iron is easy to machine but cannot withstand a heavy shock. Gray cast iron consists of 90 to 94 percent metallic iron with a mixture of carbon, manganese, phosphorus, sulfur, and silicon. Special high-strength grades of this metal also contain 0.75 to 1.50 percent nickel and 0.25 to 0.50 percent chromium or 0.25 to 1.25 percent molybdenum. Commercial gray iron has 2.50 to 4.50 percent carbon. About 1 percent of the carbon is combined with the iron, while about 2.75 percent remains in the free or graphitic state. In making gray cast iron, the silicon content is usually increased, since this allows the formation of graphitic carbon. The combined carbon (iron carbide), which is a small percentage of the total carbon present in cast iron, is known as cementite. In general, the more free carbon (graphitic carbon) present in cast iron, the lower the combined carbon content and the softer the iron.
1. Appearance test. The unmachined surface of gray cast iron castings is a very dull gray in color and may be somewhat roughened by the sand mold used in casting the part. Cast iron castings are rarely machined all over. Unmachined castings may be ground in places to remove rough edges.
2. Fracture test. Nick a corner all around with a chisel or hacksaw and strike the corner with a sharp blow of the hammer. The dark gray color of the broken surface is caused by fine black specks of carbon present in the form of graphite. Cast iron breaks short when fractured. Small, brittle chips made with a chisel break off as soon as they are formed.
3. Spark test. A small volume of dull-red sparks that follow a straight line close to the wheel are given off when this metal is spark tested. These break up into many fine, repeated spurts that change to a straw color.
4. Torch test. The torch test results in a puddle of molten metal that is quiet and has a jelly like consistency. When the torch flame is raised, the depression in the surface of the molts-puddle disappears instantly. A heavy, tough film forms on the surface as it melts. The molten puddle takes time to harden and gives off no sparks.
(g) White cast iron. When gray cast iron is heated to the molten state, the carbon completely dissolves in the iron, probably combining chemically with it. If this molten metal is cooled quickly, the two elements remain in the combined state, and white cast iron is formed. The carbon in this type of iron measures above 2.5 to 4.5 percent by weight, and is referred to as combined carbon. White cast iron is very hard and brittle, often impossible to machine, and has a silvery white fracture.
(h) Malleable cast iron. Malleable cast iron is made by heating white cast iron from 1400 to 1700°F (760 and 927°C) for abut 150 hours in boxes containing hematite ore or iron scale. This heating causes a part of the combined carbon to change into the free or uncombined state. This free carbon separates in a different way from carbon in gray cast iron and is called temper carbon. It exists in the form of small, rounded particles of carbon which give malleable iron castings the ability to bend before breaking and to withstand shock better than gray cast iron. The castings have properties more like those of pure iron: high strength, ductility, toughness, and ability to resist shock. Malleable cast iron can be welded and brazed. Any welded part should be annealed after welding.
1. Appearance test. The surface of malleable cast iron is very much like gray cast iron, but is generally free from sand. It is dull gray and somewhat lighter in color than gray cast iron.
2. Fracture test. When malleable cast iron is fractured, the central portion of the broken surface is dark gray with a bright, steel-like band at the edges. The appearance of the fracture may best be described as a picture frame. When of good quality, malleable cast iron is much tougher than other cast iron and does not break short when nicked.
3. Spark test. When malleable cast iron is ground, the outer, bright layer gives off bright sparks like steel. As the interior is reached, the sparks quickly change to a dull-red color near the wheel. These sparks from the interior section are very much like those of cast iron; however, they are somewhat longer and are present in large volume.
4. Torch test. Molten malleable cast iron boils under the torch flame. After the flame has been withdrawn, the surface will be full of blowholes. When fractured, the melted parts are very hard and brittle, having the appearance of white cast iron (they have been changed to white or chilled iron by melting and fairly rapid cooling). The outside, bright, steel-like band gives off sparks, but the center does not.
(3) Steel.
(a) General. A form of iron, steel contains less carbon than cast iron, but considerably more than wrought iron. The carbon content is from 0.03 to 1.7 percent. Basic carbon steels are alloyed with other elements, such as chromium and nickel, to increase certain physical properties of the metal.
(b) Uses. Steel is used to make nails, rivets, gears, structural steel, roles, desks, hoods, fenders, chisels, hammers, etc.
(c) Capabilities. Steel can be machined, welded, and forged, all to varying degrees, depending on the type of steel.
(d) Limitations. Highly alloyed steel is difficult to produce.
(e) Properties. Steel has tensile strength of 45,000 psi (310,275 kPa) for low-carbon steel, 80,000 psi (551,600 kPa) for medium-carbon steel, 99,000 psi (692,605 kPa) for high-carbon steel, and 150,000 psi (1,034,250 kPa) for alloyed steel; and a melting point of 2800° F (1538°C).
(f) Low-carbon steel (carbon content up to 0.30 percent. This steel is soft and ductile, and can be rolled, punched, sheared, and worked when either hot or cold. It is easily machined and can readily be welded by all methods. It does not harden to any great amount; however, it can easily be case hardened.
1. Appearance test. The appearance of the steel depends upon the method of preparation rather than upon composition. Cast steel has a relatively rough, dark-gray surface, except where it has been machined. Rolled steel has fine surface lines running in one direction. Forged steel is usually recognizable by its shape, hammer marks, or fins.
2. Fracture test. When low-carbon steel is fractured, the color is bright crystalline gray. It is tough to chip or nick. Low carbon steel, wrought iron, and steel castings cannot be hardened.
3. Spark test. The steel gives off sparks in long yellow-orange streaks, brighter than cast iron, that show some tendency to burst into white, forked sparklers.
4. Torch test. The steel gives off sparks when melted, and hardens almost instantly.
(g) Medium-carbon steel (carbon content ranging from 0.30 to 0.50 percent). This steel may be heat-treated after fabrication. It is used for general machining and forging of parts that require surface hardness and strength. It is made in bar form in the cold-rolled or the normalized and annealed condition. During welding, the weld zone will become hardened if cooled rapidly and must be stress-relieved after welding.
(h) High-carbon steel (carbon content ranging from 0.50 to 0.90 percent). This steel is used for the manufacture of drills, taps, dies, springs, and other machine tools and hand tools that are heat treated after fabrication to develop the hard structure necessary to withstand high shear stress and wear. It is manufactured in bar, sheet, and wire forms, and in the annealed or normalized condition in order to be suitable for machining before heat treatment. This steel is difficult to weld because of the hardening effect of heat at the welded joint.
1. Appearance test. The unfinished surface of high-carbon steel is dark gray and similar to other steel. It is more expensive, and is usually worked to produce a smooth surface finish.
2. Fracture test. High-carbon steel usually produces a very fine-grained fracture, whiter than low-carbon steel. Tool steel is harder and more brittle than plate steel or other low-carbon material. High-carbon steel can be hardened by heating to a good red and quenching in water.
3. Spark test. High-carbon steel gives off a large volume of bright yellow-orange sparks.
4. Torch test. Molten high-carbon steel is brighter than lowcarbon steel, and the melting surface has a porous appearance. It sparks more freely than low-carbon (mild) steels, and the sparks are whiter.
(i) High carbon tool steel. Tool steel (carbon content ranging from 0.90 to 1.55 percent) is used in the manufacture of chisels, shear blades, cutters, large taps, wood-turning tools, blacksmith's tools, razors, and similar parts where high hardness is required to maintain a sharp cutting edge. It is difficult to weld due to the high carbon content. A spark test shows a moderately large volume of white sparks having many fine, repeating bursts.
(4) Cast steel.
(a) General. Welding is difficult on steel castings containing over 0.30 percent carbon and 0.20 percent silicon. Alloy steel castings containing nickel, molybdenum, or both of these metals, are easily welded if the carbon content is low. Those containing chromium or vanadium are more difficult to weld. Since manganese steel is nearly always used in the form of castings, it is also considered with cast steel. Its high resistance to wear is its most valuable property.
(b) Appearance test. The surface of cast steel is brighter than cast or malleable iron and sometimes contains small, bubble-like depressions.
(c) Fracture test. The color of a fracture in cast steel is bright crystalline gray. This steel is tough and does not break short. Steel castings are tougher than malleable iron, and chips made with a chisel curl up more. Manganese steel, however, is so tough that is cannot be cut with a chisel nor can it be machined.
(d) Spark test. The sparks created from cast steel are much brighter than those from cast iron. Manganese steel gives off marks that explode, throwing off brilliant sparklers at right angles to the original-path of the spark:
(e) Torch test. When melted, cast steel sparks and hardens quickly.
(5) Steel forgings.
(a) General. Steel forgings may be of carbon or alloy steels. Alloy steel forgings are harder and more brittle than low carbon steels.
(b) Appearance test. The surface of steel forgings is smooth. Where the surface of drop forgings has not been finished, there will be evidence of the fin that results from the metal squeezing out between the two forging dies. This fin is removed by the trimming dies, but enough of the sheared surface remains for identification. All forgings are covered with reddish brown or black scale, unless they have been purposely cleaned.
(c) Fracture test. The color of a fracture in a steel forging varies from bright crystalline to silky gray. Chips are tough; and when a sample is nicked, it is harder to break than cast steel and has a finer grain. Forgings may be of low-or high-carbon steel or of alloy steel. Tool steel is harder and more brittle than plate steel or other low-carbon material. The fracture is usually whiter and finer grained. Tool steel can be hardened by heating to a good red and then quenching in water. Low-carbon steel, wrought iron, and steel castings cannot be usefully hardened.
(d) Spark test. The sparks given off are long, yellow-orange streamers and are typical steel sparks. Sparks from high-carbon steel (machinery and tool steel) are much brighter than those from low-carbon steel.
(e) Torch test. Steel forgings spark when melted, and the sparks increase in number and brightness as the carbon content becomes greater.
(6) Alloy steel.
(a) General. Alloy steel is frequently recognizable by its use. There are many varieties of alloy steel used in the manufacture of Army equipment. They have greater strength and durability than carbon steel, and a given strength is secured with less material weight. Manganese steel is a special alloy steel that is always used in the cast condition (see cast steel, above).
Nickel, chromium, vanadium, tungsten, molybdenum, and silicon are the most common elements used in alloy steel.
1. Chromium is used as an alloying element in carbon steels to increase hardenability, corrosion resistance, and shock resistance. It imparts high strength with little loss in ductility.
2. Nickel increases the toughness, strength, and ductility of steels, and lowers the hardening temperatures so than an oil quench, rather than a water quench, is used for hardening.
3. Manganese is used in steel to produce greater toughness, wear resistance, easier hot rolling, and forging. An increase in manganese content decreases the weldability of steel.
4. Molybdenum increases hardenability, which is the depth of hardening possible through heat treatment. The impact fatigue property of the steel is improved with up to 0.60 percent molybdenum. Above 0.60 percent molybdenum, the impact fatigue property is impaired. Wear resistance is improved with molybdenum content above 0.75 percent. Molybdenum is sometimes combined with chromium, tungsten, or vanadium to obtain desired properties.
5. Titanium and columbium (niobium) are used as additional alloying agents in low-carbon content, corrosion resistant steels. They support resistance to intergranular corrosion after the metal is subjected to high temperatures for a prolonged time period.
6. Tungsten, as an alloying element in tool steel, produces a fine, dense grain when used in small quantities. When used in larger quantities, from 17 to 20 percent, and in combination with other alloys, it produces a steel that retains its hardness at high temperatures.
7. Vanadium is used to help control grain size. It tends to increase hardenability and causes marked secondary hardness, yet resists tempering. It is also added to steel during manufacture to remove oxygen.
8. Silicon is added to steel to obtain greater hardenability and corrosion resistance, and is often used with manganese to obtain a strong, tough steel. High speed tool steels are usually special alloy compositions designed for cutting tools. The carbon content ranges from 0.70 to 0.80 percent. They are difficult to weld except by the furnace induction method.
9. High yield strength, low alloy structural steels (often referred to as constructional alloy steels) are special low carbon steels containing specific small amounts of alloying elements. These steels are quenched and tempered to obtain a yield strength of 90,000 to 100,000 psi (620,550 to 689,500 kPa) and a tensile strength of 100,000 to 140,000 psi (689,500 to 965,300 kPa), depending upon size and shape. Structural members fabricated of these high strength steels may have smaller cross sectional areas than common structural steels, and still have equal strength. In addition, these steels are more corrosion and abrasion resistant. In a spark test, this alloy appears very similar to the low carbon steels.
NOTE
This type of steel is much tougher than low carbon steels, and shearing machines must have twice the capacity required for low carbon steels.
(b) Appearance test. Alloy steel appear the same as drop-forged steel.
(c) Fracture test. Alloy steel is usually very close grained; at times the fracture appears velvety.
(d) Spark test. Alloy steel produces characteristic sparks both in color and shape. Some of the more common alloys used in steel and their effects on the spark stream are as follows:
1. Chromium. Steels containing 1 to 2 percent chromium have no outstanding features in the spark test. Chromium in large amounts shortens the spark stream length to one-half that of the same steel without chromium, but does not appreciably affect the stream's brightness. Other elements shorten the stream to the same extent and also make it duller. An 18 percent chromium, 8 percent nickel stainless steel produces a spark similar to that of wrought iron, but only half as long. Steel containing 14 percent chromium and no nickel produces a shorter version of the low-carbon spark. An 18 percent chromium, 2 percent carbon steel (chromium die steel) produces a spark similar to that of carbon tool steel, but one-third as long.
2. Nickel. The nickel spark has a short, sharply defined dash of brilliant light just before the fork. In the amounts found in S. A. E. steels, nickel can be recognized only when the carbon content is so low that the bursts are not too noticeable.
3. High chromium-nickel alloy (stainless) steels. The sparks given off during a spark test are straw colored near the grinding wheel and white near the end of the streak. There is a medium volume of streaks having a moderate number of forked bursts.
4. Manganese. Steel containing this element produces a spark similar to a carbon steel spark. A moderate increase in manganese increases the volume of the spark stream and the force of the bursts. Steel containing more than the normal amount of manganese will spark in a manner similar to high-carbon steel with low manganese content.
5. Molybdenum. Steel containing this element produces a characteristic spark with a detached arrowhead similar to that of wrought iron. It can be seen even in fairly strong carbon bursts. Molybdenum alloy steel contains nickel, chromium, or both.
6. Molybdenum with other elements. When molybdenum and other elements are substituted for some of the tungsten in high-speed steel, the spark stream turns orange. Although other elements give off a red spark, there is enough difference in their color to tell them from a tungsten spark.
7. Tungsten. Tungsten will impart a dull red color to the spark stream near the wheel. It also shortens the spark stream, decreases the size, or completely eliminates the carbon burst. Steel containing 10 percent tungsten causes short, curved, orange spear points at the end of the carrier lines. Still lower tungsten content causes small white bursts to appear at the end of the spear point. Carrier lines may be anything from dull red to orange in color, depending on the other elements present, if the tungsten content is not too high.
8. Vanadium. Alloy steels containing vanadium produce sparks with a detached arrowhead at the end of the carrier line similar to those arising from molybdenum steels. The spark test is not positive for vanadium steels.
9. High speed tool steels. A spark test in these steels will impart a few long; forked sparks which are red near the wheel, and straw-colored near the end of the spark stream.
(7) Special steel. Plate steel is used in the manufacture of built-up welded structures such as gun carriages. In using nickel plate steel, it has been found that commercial grades of low-alloy structural steel of not over 0.25 percent carbon, and several containing no nickel at all, are better suited to welding than those with a maximum carbon content of 0.30 percent. Armorplate, a low carbon alloyed steel, is an example of this kind of plate. Such plate is normally used in the "as rolled" condition. Electric arc welding with a covered electrode may require preheating of the metal, followed by a proper stress-relieving heat treatment (post heating), to produce a structure in which the welded joint has properties equal to those of the plate metal.
e. Nonferrous metal.
(1) Aluminum (Al).
(a) General. Aluminum is a lightweight, soft, low strength metal which can easily be cast, forged, machined, formed, and welded. It is suitable only in low temperature applications, except when alloyed with specific elements. Commercial aluminum alloys are classified into two groups, wrought alloys and cast alloys. The wrought alloy group includes those alloys which are designed for mill products whose final physical forms are obtained by working the metal mechanically. The casting alloy group includes those alloys whose final shapes are obtained by allowing the molten metal to solidify in a mold.
(b) Uses. Aluminum is used as a deoxidizer and alloying agent in the manufacture of steel. Castings, pistons, torque converter pump housings, aircraft structures, kitchen utensils, railways cars, and transmission lines are made of aluminum.
(c) Capabilities. Aluminum can be cast, forged, machined, formed, and welded.
(d) Limitations. Direct metal contact of aluminum with copper and copper alloys should be avoided. Aluminum should be used in low-temperature applications.
(e) Properties. Pure aluminum has a Brinell hardness number of 17 to 27; tensile strength of 6000 to 16,000 psi (41,370 to 110,320 kPa); specific gravity of 2.7; and a melting point of 1220°F (660°C). Aluminum alloys have a Brinell hardness number of 100 to 130, and tensile strength of 30,000 to 75,000 psi (206,850 to 517,125 kPa). Generally, aluminum and aluminum alloys have excellent heat conductivity; high electrical conductivity (60 percent that of copper, volume for volume; high strength/weight ratio at room temperature; and unfairly corrosion resistant.
(f) Appearance test. Aluminum is light gray to silver in color, very bright when polished, dull when oxidized, and light in weight. Rolled and sheet aluminum materials are usually pure metal. Castings are alloys of aluminum with other metals, usually zinc, copper, silicon, and sometimes iron and magnesium. Wrought aluminum alloys may contain chromium, silicon, magnesium, or manganese. Aluminum strongly resembles magnesium in appearance. Aluminum is distinguished from magnesium by the application of a drop of silver nitrate solution on each surface. The silver nitrate will not react with the aluminum, but leaves a black deposit of silver on the magnesium.
(g) Fracture test. A fracture in rolled aluminum sections shows a smooth, bright structure. A fracture in an aluminum casting shins a bright crystalline structure.
(h) Spark test. No sparks are given off from aluminum.
(i) Torch test. Aluminum does not turn red before melting. It holds its shape until almost molten, then collapses (hot shorts) suddenly. A heavy film of white oxide forms instantly on the molten surface.
(2) Chromium (Cr).
(a) General. Chromium is an alloying agent used in steel, cast iron, and nonferrous alloys of nickel, copper, aluminum, and cobalt. It is hard, brittle, corrosion resistant, can be welded, machined, forged, and is widely used in electroplating. Chromium is not resistant to hydrochloric acid and cannot be used in its pure state because of its difficulty to work.
(b) Uses. Chromium is one of the most widely used alloys. It is used as an alloying agent in steel and cast iron (0.25 to 0.35 percent) and in nonferrous alloys of nickel, copper, aluminum, and cobalt. It is also used in electroplating for appearance and wear, in powder metallurgy, and to make mirrors and stainless steel.
(c) Capabilities. Chromium alloys can be welded, machined, and forged. Chromium is never used in its pure state.
(d) Limitations. Chromium is not resistant to hydrochloric acid, and cannot be used in the pure state because of its brittleness and difficulty to work.
(e) Properties (pure). Chromium has a specific gravity of 7.19; a melting point of 3300°F (1816°C); Brinell hardness number of 110 to 170; is resistant to acids other than hydrochloric; and is wear, heat, and corrosion resistant.
(3) Cobalt (Co).
(a) General. Cobalt is a hard, white metal similar to nickel in appearance, but has a slightly bluish cast.
(b) Uses. Cobalt is mainly used as an alloying element in permanent and soft magnetic materials, high-speed tool bits and cutters, high-temperature, creep-resisting alloys, and cemented carbide tools, bits, and cutters. It is also used in making insoluble paint pigmnts and blue ceramic glazes. In the metallic form, cobalt does not have many uses. However, when combined with other elements, it is used for hard facing materials.
(c) Capabilities. Cobalt can be welded, machined (limited), and cold-drawn.
(d) Limitations. Cobalt must be machined with cemented carbide cutters. Welding high carbon cobalt steel often causes cracking.
(e) Properties. Pure cobalt has a tensile strength of 34,000 psi (234,430 kPa); Brinell hardness number of 125; specific gravity of 8.9; and a melting point of 2720°F (1493°C). Cobalt alloy (Stellite 21) has a tensile strength of 101,000 psi (696,395 kPa) and is heat and corrosion resistant.
(4) Copper (Cu).
(a) General. Copper is a reddish metal, is very ductile and malleable, and has high electrical and heat conductivity. It is used as a major element in hundreds of alloys. Commercially pure copper is not suitable for welding. Though it is very soft, it is very difficult to machine due to its high ductility. Beryllium copper contains from 1.50 to 2.75 percent beryllium. It is ductile when soft, but loses ductility and gains tensile strength when hardened. Nickel copper contains either 10, 20, or 30 percent nickel. Nickel alloys have moderately high to high tensile strength, which increases with the nickel content. They are moderately hard, quite tough, and ductile. They are very resistant to the erosive and corrosive effects of high velocity sea water, stress corrosion, and corrosion fatigue. Nickel is added to copper zinc alloys (brasses) to lighten their color; the resultant alloys are called nickel silver. These alloys are of two general types, one type containing 65 percent or more copper and nickel combined, the other containing 55 to 60 percent copper and nickel combined. The first type can be cold worked by such operations as deep drawing, stamping, and spinning. The second type is much harder end is not processed by any of the cold working methods. Gas welding is the preferred process for joining copper and copper alloys.
(b) Uses. The principal use of commercially pure copper is in the electrical industry where it is made into wire or other such conductors. It is also used in the manufacture of nonferrous alloys such as brass, bronze, and Monel metal. Typical copper products are sheet roofing, cartridge cases, bushings, wire, bearings, and statues.
(c) Capababilities. Copper can be forged, cast, and cold worked. It can also be welded, but its machinability is only fair. Copper alloys can be welded.
(d) Limitations. Electrolytic tough pitch copper cannot be welded satisfactorily. Pure copper is not suitable for welding and is difficult to machine due to its ductility.
(e) Properties. Pure copper is nonmagnetic; has a Brinell hardness number of 60 to 110; a tensile strength of 32,000 to 60,000 psi (220,640 to 413,700 kPa); specific gravity of 8.9; melting point of 1980°F (1082°C); and is corrosion resistant. Copper alloys have a tensile strength of 50,000 to 90,000 psi (344,750 to 620,550 kPa) and a Brinell hardness number of 100 to 185.
(f) Appearance test. Copper is red in color when polished, and oxidizes to various shades of green.
(g) Fracture test. Copper presents a smooth surface when fractured, which is free from crystalline appearance.
(h) Spark test. Copper gives off no sparks.
(i) Torch test. Because copper conducts heat rapidly, a larger flame is required to produce fusion of copper than is needed for the same size piece of steel. Copper melts suddenly and solidifies instantly. Copper alloy, containing small amounts of other metals, melts more easily and solidifies more slowly than pure copper.
(j) Brass and bronze. Brass, an alloy of copper and zinc (60 to 68 percent copper and 32 to 40 percent zinc), has a low melting point and high heat conductivity. There are several types of brass, such as naval, red, admiralty, yellow, and commercial. All differ in copper and zinc content; may be alloyed with other elements such as lead, tin, manganese, or iron; have good machinability; and can be welded. Bronze is an alloy of copper and tin and may contain lead, zinc, nickel, manganese, or phosphorus. It has high strength, is rust or corrosion resistant, has good machinability, and can be welded.
1. Appearance test. The color of polished brass and bronze varies with the composition from red, almost like copper, to yellow brass. They oxidize to various shades of green, brown, or yellow.
2. Fracture test. The surface of fractured brass or bronze ranges from smooth to crystalline, depending upon composition and method of preparation; i. e., cast, rolled, or forged.
3. Spark test. Brass and bronze give off no sparks.
4. Torch test. Brass contains zinc, which gives off white fumes when it is melted. Bronze contains tin. Even a slight amount of tin makes the alloy flow very freely, like water. Due to the small amount of zinc or tin that is usually present, bronze may fume slightly, but never as much as brass.
(k) Aluminum bronze.
1. Appearance test. When polished, aluminum bronze appears a darker yellow than brass.
2. Fracture test. Aluminum bronze presents a smooth surface when fractured.
3. Spark test. Aluminum bronze gives off no sparks.
4. Torch test. Welding aluminum bronze is very difficult. The surface is quickly covered with a heavy scum that tends to mix with the metal and is difficult to remove.
(5) Lead (Pb).
CAUTION
Lead dust and fumes are poisonous. Exercise extreme care when welding lead, and use personal protective equipment.
(a) General. Lead is a heavy, soft, malleable metal with low melting point, low tensile strength, and low creep strength. It is resistant to corrosion from ordering atmosphere, moisture, and water, and is effective against many acids. Lead is well suited for cold working and casting. The low melting point of lead makes the correct welding rod selection very important.
(b) Uses. Lead is used mainly in the manufacture of electrical equipment such as lead-coated power and telephone cables, and storage batteries. It is also used in building construction in both pipe and sheet form, and in solder. Zinc alloys are used in the manufacture of lead weights, bearings, gaskets, seals, bullets, and shot. Many types of chemical compounds are produced from lead; among these are lead carbonate (paint pigment) and tetraethyl lead (antiknock gasoline). Lead is also used for X-ray protection (radiation shields). Lead has more fields of application than any other metal.
(c) Capabilities. Lead can be cast, cold worked, welded, and machined. It is corrosion, atmosphere, moisture, and water resistant, and is resistant to many acids.
(d) Limitations. Lead has low strength with heavy weight. Lead dust and fumes are very poisonous.
(e) Properties. Pure lead has tensile strength of 2500 to 3000 psi (17,237.5 to 20,685 kPa); specific gravity of 11.3; and a melting point of 620°F (327°C). Alloy lead B32-467 has tensile strength of 5800 psi (39,991 kPa). Generally, lead has low electrical conductivity; is self-lubricating; is malleable; and is corrosion resistant.
(6) Magnesium (Mg).
(a) General. Magnesium is an extremely light metal, is white in color, has a low melting point, excellent machinability, and is weldable. Welding by either the arc or gas process requires the use of a gaseous shield. Magnesium is moderately resistant to atmospheric exposure, many chemicals such as alkalies, chromic and hydrofluoric acids, hydrocarbons, and most alcohols, phenols, esters, and oils. It is nonmagnetic. Galvanic corrosion is an important factor in any assembly with magnesium.
(b) Uses. Magnesium is used as a deoxidizer for brass, bronze, nickel, and silver. Because of its light weight, it is used in many weight-saving applications, particularly in the aircraft industry. It is also used in the manufacture and use of fireworks for railroad flares and signals, and for military purposes. Magnesium castings are used for engine housings, blowers, hose pieces, landing wheels, and certain parts of the fuselage of aircraft. Magnesium alloy materials are used in sewing machines, typewriters, and textile machines.
(c) Capabilities. Magnesium can be forged, cast, welded, and machined.
(d) Limitations. Magnesium in fine chip form will ignite at low temperatures (800 to 1200°F (427 to 649°C)). The flame can be mothered with suitable materials such as carbon dioxide (CO2), foam, and sand.
(e) Properties. Pure magnesium has tensile strength of 12,000 psi (82,740 kPa) (cast) and tensile strength of 37,000 psi (255,115 kPa) (rolled); Brinell hardness number of 30 (cast) and 50 (rolled); specific gravity of 1.7; and a melting point of 1202°F (650°C). Magnesium alloy has Brinell hardness number of 72 (hard) and 50 (forged); and tensile strength of 42,000 psi (289,590 kPa) (hard) and 32,000 psi (220,640 kPa) (forged).
(f) Appearance test. Magnesium resembles aluminum in appearance. The polished surface is silver-white, but quickly oxidizes to a grayish film. Like aluminum, it is highly corrosion resistant and has a good strength-to-weight ratio, but is lighter in weight than aluminum. It has a very low kindling point and is not very weldable, except when it is alloyed with manganese and aluminum. Magnesium is distinguished from aluminum by the use of a silver nitrate solution. The solution does not react with aluminum, but leaves a black deposit of silver on magnesium. Magnesium is produced in large quantities from sea water. It has excellent machinability, but special care must be used when machining because of its low kindling point.
(g) Fracture test. Magnesium has a rough surface with a fine grain structure.
(h) Spark test. No sparks are given off.
CAUTION
Magnesium may ignite and burn when heated in the open atmosphere.
(i) Torch test. Magnesium oxidizes rapidly when heated in open air, producing an oxide film which is insoluble in the liquid metal. A fire may result when magnesium is heated in the open atmosphere. As a safety precaution, magnesium should be melted in an atmosphere of inert gas.
(7) Manganese (Mn).
(a) General. Pure manganese has a relatively high tensile strength, but is very brittle. Manganese is used as an alloying agent in steel to deoxidize and desulfurize the metal. In metals other than steel, percentages of 1 to 15 percent manganese will increase the toughness and the hardenability of the metal involved.
(b) Uses. Manganese is used mainly as an alloying agent in making steel to increase tensile strength. It is also added during the steel-making process to remove sulfur as a slag. Austenitic manganese steels are used for railroad track work, power shovel buckets, and rock crushers. Medium-carbon manganese steels are used to make car axles and gears.
(c) Capabilities. Manganese can be welded, machined, and cold-worked.
(d) Limitations. Austenitic manganese steels are best machined with cemented carbide, cobalt, and high-speed steel cutters.
(e) Properties. Pure manganese has tensile strength of 72,000 psi (496,440 kPa) (quenched) Brinell hardness number of 330; specific gravity of 7.43: a melting point of 2270°F (1243°C); and is brittle. Manganese alloy has a tensile strength of 110,000 psi (758,450 kPa). Generally, manganese is highly polishable and brittle.
(8) Molybdenum (Mo).
(a) General. Pure molybdenum has a high tensile strength and is very resistant to heat. It is principally used as an alloying agent in steel to increase strength, hardenability, and resistance to heat.
(b) Uses. Molybdenum is used mainly as an alloy. Heating elements, switches, contacts, thermocouplers, welding electrodes, and cathode ray tubes are made of molybdenum.
(c) Capabilities. Molybdenum can be swaged, rolled, drawn, or machined.
(d) Limitations. Molybdenum can only be welded by atomic hydrogen arc, or butt welded by resistance heating in vacuum. It is attacked by nitric acid, hot sulfuric acid, and hot hydrochloric acid.
(e) Properties. Pure molybdenum has a tensile strength of 100,000 psi (689,500 kPa) (sheet) and 30,000 Psi (206,850 kPa) (wire); Brinell hardness number of 160 to 185; specific gravity of 10.2; meting point of 4800°F (2649°C); retains hardness and strength at high temperatures; and is corrosion resistant.
(9) Nickel (Ni).
(a) General. Nickel is a hard, malleable, ductile metal. As an alloy, it will increase ductility, has no effect on grain size, lowers the critical point for heat treatment, aids fatigue strength, and increases impact values in low temperature operations. Both nickel and nickel alloys are machinable and are readily welded by gas and arc methods.
(b) Uses. Nickel is used in making alloys of both ferrous and nonferrous metal. Chemical and food processing equipment, electrical resistance heating elements, ornamental trim, and parts that must withstand elevated temperatures are all produced from nickel-containing metal. Alloyed with chromium, it is used in the making of stainless steel.
(c) Capabilities. Nickel alloys are readily welded by either the gas or arc methods. Nickel alloys can be machined, forged, cast, and easily formed.
(d) Limitations. Nickel oxidizes very slowly in the presence of moisture or corrosive gases.
(e) Properties. Pure nickel has tensile strength of 46,000 psi (317,170 kPa); Brinell hardness number 220; specific gravity of 8.9; and melting point of 2650°F (1454°C). Nickel alloys have Brinell hardness number of 140 to 230. Monel-forged nickel has tensile strength of 100,000 psi (689,500 kPa), and high strength and toughness at high temperatures.
(f) Appearance. Pure nickel has a grayish white color.
(g) Fracture. The fracture surface of nickel is smooth and fine grained.
(h) Spark test. In a spark test, nickel produces a very small amount of short, orange streaks which are generally wavy.
(i) Monel metal. Monel metal is a nickel alloy of silver-white color containing about 67.00 percent nickel, 29.00 to 80.00 percent copper, 1.40 percent iron, 1.00 percent manganese, 0.10 percent silicon, and 0.15 percent carbon. In appearance, it resembles untarnished nickel. After use, or after contact with chemical solutions, the silver-white color takes on a yellow tinge, and some of the luster is lost. It has a very high resistance to corrosion and can be welded.
(10) Tin (Sn).
(a) General. Tin is a very soft, malleable, somewhat ductile, corrosion resistant metal having low tensile strength and high crystalline structure. It is used in coating metals to prevent corrosion.
(b) Uses. The major application of tin is in coating steel. It serves as the best container for preserving perishable focal. Tin, in the form of foil, is often used in wrapping food products. A second major use of tin is as an alloying element. Tin is alloyed with copper to produce tin brass and bronze, with lead to produce solder, and with antimony and lead to form babbitt.
(c) Capabilities. Tin can be die cast, cold worked (extruded), machined, and soldered.
(d) Limitations. Tin is not weldable.
(e) Properties. Pure tin has tensile strength of 2800 psi (19,306 kPa); specific gravity of 7.29; melting point of 450°F (232°C); and is corrosion resistant. Babbitt alloy tin has tensile strength of 10,000 psi (68,950 kPa) and Brinell hardness number of 30.
(f) Appearance. Tin is silvery white in color.
(g) Fracture test. The fracture surface of tin is silvery white and fairly smooth.
(h) Spark test. Tin gives off no sparks in a spark test.
(i) Torch test. Tin melts at 450°F (232°C), and will boil under the torch.
(11) Titanium (Ti).
(a) General. Titanium is a very soft, silvery white, medium-strength metal having very good corrosion resistance. It has a high strength to weight ratio, and its tensile strength increases as the temperature decreases. Titanium has low impact and creep strengths, as well as seizing tendencies, at temperatures above 800°F (427°C).
(b) Uses. Titanium is a metal of the tin group which occurs naturally as titanium oxide or in other oxide forms. The free element is separated by heating the oxide with aluminum or by the electrolysis of the solution in calcium chloride. Its most important compound is titanium dioxide, which is used widely in welding electrode coatings. It is used as a stabilizer in stainless steel so that carbon will not be separated during the welding operation. It is also used as an additive in alloying aluminum, copper, magnesium, steel, and nickel; making powder for fireworks; and in the manufacture of turbine blades, aircraft firewalls, engine nacelles, frame assemblies, ammunition tracks, and mortar base plates.
(c) Capabilities. Titanium can be machined at low speeds and fast feeds; formal; spot-and seam-welded, and fusion welded using inert gas.
(d) Limitations. Titanium has low impact strength, and low creep strength at high temperatures (above 800°F (427°C)). It can only be cast into simple shapes, and it cannot be welded by any gas welding process because of its high attraction for oxygen. Oxidation causes this metal to become quite brittle. The inert gas welding process is recommended to reduce contamination of the weld metal.
(e) Properties. Pure titanium has a tensile strength of 100,000 psi; Brinell hardness number of 200; specific gravity of 4.5; melting point of 3300°F (1851°C); and good corrosion resistance. Alloy titanium has a Brinell hardness number of 340; tensile strength of 150,000 psi; and a high strength/weight ratio (twice that of aluminum alloy at 400°F (204°C)).
(f) Appearance test. Titanium is a soft, shiny, silvery-white metal burns in air and is the only element that burns in nitrogen. Titanium alloys look like steel, and can be distinguished from steel by a copper sulfate solution. The solution will not react with titanium, but will leave a coating of copper on steel.
(g) Spark test. The sparks given off are large, brilliant white, and of medium length.
(12) Tungsten (W).
(a) General. Tungsten is a hard, heavy, nonmagnetic metal which will melt at approximately 6150°F (3400°C).
(b) Uses. Tungsten is used in making light bulb filaments, phonograph needles, and as an alloying agent in production of high-speed steel, armorplate, and projectiles. It is also used as an alloying agent in nonconsumable welding electrodes, armor plate, die and tool steels, and hard metal carbide cutting tools.
(c) Capabilities. Tungsten can be cold and hot drawn.
(d) Limitations. Tungsten is hard to machine, requires high temperatures for melting, and is produced by powered metallurgy (sintering process).
(e) Properties. Tungsten has a melting point of 6170 ± 35°F (3410 ± 19°C); is ductile; has tensile strength of 105,000 psi (723,975 kPa); a specific gravity of 19.32; thermal conductivity of 0.397; a Brinell hardness number of 38; and is a dull white color.
(f) Appearance. Tungsten is steel gray in color.
(g) Spark test. Tungsten produces a very small volume of short, straight, orange streaks in a spark test.
(13) Zinc (Zn).
(a) General. Zinc is a medium low strength metal having a very low melting point. Ito is easy to machine, but coarse grain zinc should be heated to approximately 180°F (82°C) to avoid cleavage of crystals. Zinc can be soldered or welded if it is properly cleaned and the heat input closely controlled.
(b) Uses.
1. Galvanizing metal is the largest use of zinc and is done by dipping the part in molten zinc or by electroplating it. Examples of items made in this way are galvanized pipe, tubing, sheet metal, wire, nails, and bolts. Zinc is also used as an alloying element in producing alloys such as brass and bronze. Those alloys that are made up primarily of zinc itself.
2. Typical parts made with zinc alloy are die castings, toys, ornaments, building equipment, carburetor and fuel pump bodies, instrument panels, wet and dry batteries, fuse plugs, pipe organ pipes, munitions, cooking utensils, and flux. Other forms of zinc include zinc oxide and zinc sulfide, widely used in paint and rubber, and zinc dust, which is used in the manufacture of explosives and chemical agents.
(c) Capabilities. Zinc can be cast, cold worked (extruded), machined, and welded.
(d) Limitations. Do not use zinc die castings in continuous contact with steam.
(e) Properties. Zinc has a tensile strength of 12,000 psi (82,740 kPa) (cast) and 27,000 psi (186,165 kPa) (rolled); a specific gravity of 7.1; a melting point of 790°F (421°C); is corrosion resistant; and is brittle at 220°F (104°C).
(f) Appearance. Both zinc and zinc alloys are blue-white in color when polished, and oxidize to gray.
(g) Fracture test. Zinc fractures appear somewhat granular.
(h) Spark test. Zinc and zinc alloys give off no sparks in a spark test.
(i) Zinc die castings.
1. Appearance test. Die castings are usually alloys of zinc, aluminum, magnesium, lead, and tin. They are light in weight, generally silvery white in color (like aluminum), and sometimes of intricate design. A die-cast surface is much smoother than that of a casting made in sand, and is almost as smooth as a machined surface. Sometimes, die castings darkened by use may be mistaken for malleable iron when judged simply by looks, but the die casting is lighter in weight and softer.
2. Fracture test. The surface of a zinc die casting is white and has a slight granular structure.
3. Spark test. Zinc die castings give off no sparks.
4. Torch test. Zinc die castings can be recognized by their low melting temperatures. The metal boils when heated with the oxyacetylene flame. A die casting, after thorough cleaning, can be welded with a carburizing flame using tin or aluminum solders as filler metal. If necessary, the die-cast part can be used as a pattern to make a new brass casting.
(14) White metal die castings.
(a) General. These are usually made with alloys of aluminum, lead, magnesium, or tin. Except for those made of lead and tin, they are generally light in weight and white in color.
(b) Appearance. The surface is much smoother than that produced by castings made in sand.
(c) Fracture test. Fractured surface is white and somewhat granular.
(d) Spark test. No sparks given off in a spark test.
(e) Torch test. Melting points are low, and the metal boils under the torch.
Authorization Letter
|