FCAW (Flux Cored Arc Welding) /MIG (Metal Inert Gas) / CO2
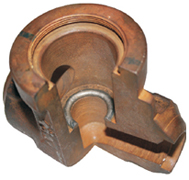 |
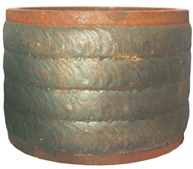 |
MIg Harfacing |
Hardbanding |
Flux-cored arc welding (FCAW) is a common arc welding process. FCAW requires a continuously fed consumable tubular electrode containing a flux and a constant voltage or, less commonly, a constant current welding power supply. The use of an externally supplied shielding gas is optional creating the primary process variation: * FCAW-S (self-shielded or “open-arc”)* FCAW-G (gas-shielded).
MIG (Metal Inert Gas Welding) is a common arc welding process. MIG require continuously fed wire electrode in wire form & constant voltage supply. It requires an externally supplied shielding gas.
Hardfacing / Cladding
Metal parts often fail their intended use not because they fracture, but because they wear, which causes them to lose dimension and functionality. Hardfacing, also known as hard surfacing, is the application of buildup or wear-resistant weld metal to part’s surface by means of welding or joining.
Benefits of Hardfacing / Cladding
- Reduces Cost: Restoring a worn part to “as new” condition generally cost between 20-70% of a brand new replacement part.
- Prolongs Equipment Life: Service life increases of 3 to 10 times are common with properly overlaid parts.
- Reduces Downtime: Parts last longer and fewer shutdowns are required.
- Less Spare Parts Inventory: There is no need to keep numerous spare parts when worn parts can be rebuilt.
|
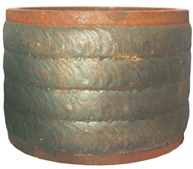 |
What base metals can be hardfaced?
- Carbon and low-alloy steels with carbon contents of less than 1 percent can be hardfaced. High-carbon alloys may require a special buffer layer.
- The following base metals can be hardfaced: Stainless steels, Manganese steels, Cast iron, and steels, Nickel-base alloys Copper-base alloys
Deposition Rate of different welding processes
Procedure |
Deposition Rate (lbs./hr.) |
FCAW |
8 to 25 |
PTA |
5 to 20 |
GMAW |
5 to 12 |
SMAW |
3 to 5 |
SAW |
8 to 25 |
GTAW |
3 to 5 |
OFW |
5 to 10 |
|
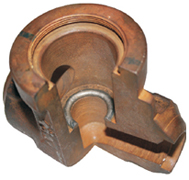
Mig Hardfacing
|
Note: It can be seen that FCAW has highest deposition rate among all common processes. |
Common Materials Used in Hardfacing / Cladding
Hardfacing are good for substrate materials that are suitable for welding, such as low-carbon steel. The most common hardfacing materials are nickel alloys and iron / chromium alloys used in wear resistance and high stress abrasion. Common materials for hardfacing are listed as follows:
Metal Alloy |
Purpose |
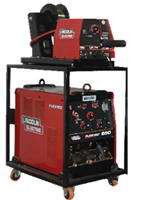 |
Cobalt-base alloy |
wear and corrosion resistance |
Copper-base alloys |
rebuilding worn machinery parts |
Iron chromium alloys |
high stress abrasion |
Manganese steel |
wear application |
Nickel-base alloys |
Metal-to-metal wear resistance |
Tool steel |
tooling, wear application |
Tungsten carbide |
high stress abrasion |
|
|
Applications:
FCAW/MIG is used for all Overlaying, Hardfacing & Cladding applications.
Typical application area of the FCAW/MIG technology are extruding machine screws, valves, valve seats of internal combustion engines (motorcar, marine, locomotive etc.), accessories for ships, petroleum chemistry and power generation, cutting tools (milling cutters, broachers, knifes), Equipment for mining, crushing, rolling, road building and tunneling, Process equipment in ceramics and cement production, Molding and forging dies, Pulp and paper industry equipment, Agricultural equipment, parts for nuclear plants, parts for chemical plant.
Advantages of FCAW
- It is a process which can be very easily automated to the highest degree, as compare to any other welding process.
- Deposition efficiency & deposition speed is very high.
- It has got very high electrical efficiency (low heat input)
- FCAW used spray transfer for deposition of metal to job.
- All the above results in a very low deformation in the job.
- It is possible to add alloys through the core (flux) to give the final desire composition.
- It is possible to work on site / outdoors.
|
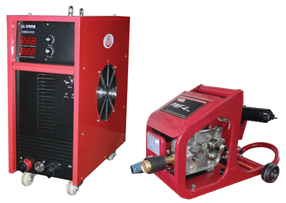 |
Model |
250 |
300 |
400 |
500 |
600 |
Input Volts |
380-440, 3Ø,
50Hz |
380-440, 3Ø,
50Hz |
380-440, 3Ø,
50Hz |
380-440, 3Ø,
50Hz |
380-440, 3Ø,
50Hz |
Output Rating |
250A |
300A |
400A |
500A |
650A |
OCV |
18-44V |
18-44V |
18-52V |
18-56V |
18-60V |
Duty cycle |
70% |
70% |
70% |
70% |
70% |
KVA |
10 |
14 |
18 |
24 |
24 |
Cooling |
Forced Air |
Forced Air |
Forced Air |
Forced Air |
Forced Air |
Insulation Class |
H |
H |
H |
H |
H |
Permissible Wire O in mm |
0.8-1.2 |
0.8-1.2 |
0.8-1.6 |
0.8-1.6 |
0.8-2.4 |
Overall Dimension (approx) in mm |
Length mm |
685 |
685 |
685 |
740 |
740 |
Width mm |
590 |
590 |
590 |
640 |
640 |
Height mm |
930 |
930 |
930 |
1030 |
1030 |
Weight (Kg) |
190 |
205 |
230 |
300 |
325 |