Plasma Transferred Arc Welding (PTA) Machines |
Arcraft is the name to turn for innovative technology. With Plasma Transferred Arc Welding we provide high productivity, high quality of powder deposits with minimum powder loss. Our advanced technology ensures significant lower cost for hardfacing , surfacing and cladding even in the most challenging area.
We are the manufacturer, supplier and exporter of Plasma Transferred Arc – PTA welding machine. |
Applications
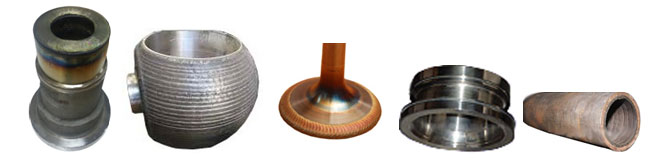
In a competition with laser surfacing the PTA technology offers much more high productivity, comparable high quality of deposits and significantly lower costs. Typical application areas of the PTA technology are:
- Extruding machine screws
- Valves
- Valve Seats of internal combustion engines (motorcar, marine, locomotive etc.)
- Accessories for ships, petroleum and chemical industries and power generation
- Cutting tools (milling cutters, broaches, knifes)
- Equipment for mining, crushing, rolling, road building and tunneling
- Process equipment in ceramics and cement production
- Moulds and forging dies
- Pulp and paper industry equipment
- Agricultural equipment
- Parts for nuclear plants
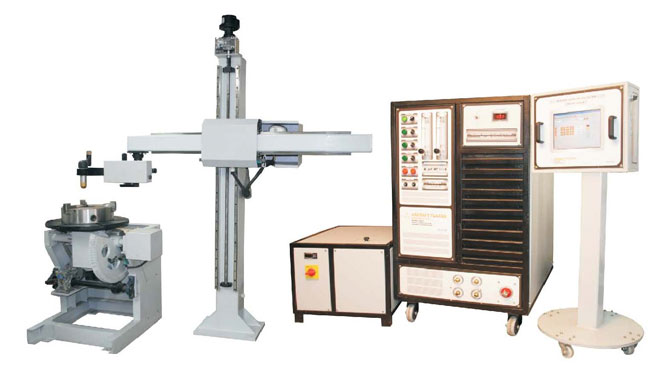
Descriptions:
- Plasma Transferred Arc (PTA) System is a high energy, inert gas welding process.
- Argon is basically used for arc plasma supply, powder transport and molten material shielding. It produces a very high quality deposit offering optimal protection with minimal dilution or deformation of the base material.
- It is a process that deposits very precise coatings of perfectly controlled alloys on mechanical parts that are subject to intense wear; significantly extending their service life.
- PTA technology is particularly effective in protection against corrosion, thermal shock and abrasion.
- A wide range of overlay alloys is available for practically any part.
- Some alloys are very hard; others are softer with hard abrasion-resistant particles dispersed in a matrix. Certain alloys are made to rebuild a part of required dimension while others are designed to be a final overlay that protects the work surface.
PTA Units
System consist of Power Source, Water Chiller, Powder Feeder, Oscillator, Welding Positioner, Controller, Column and Boom, Torch.
Check out our Manufactured PTA Machines benefits, applications, specifications and scope of supply
Features
- IGBT inverter based with analog/digital controls & integrated HF arcing system that tremendously increases its efficiency and switching characteristic
- Low Power Consumption – Optimized design of ferrite core transformer ensures low power consumption at 100% duty cycle
- Excellent Power Factor – Power factor correction capacitor ensures Power Factor of 0.95 ensuring lowest power consumption
- Stepless Power Control – Power controlled in steps in high capacity machines for extended power saving
- Easy Arc Striking – High open circuit voltage to accommodate easy arc striking
- Safety against Voltage Fluctuation & Overload – Fully protected power source against voltage fluctuation & overload added with complete safety interlocking for torch protection against gas and water failure
- Easy to Operate – Easy to operate and maintain torch head for operator's convenience
- High deposition Capacity – Highly improved torch design offers higher deposition capacity at low power output.
- Long Life of Consumables – Torch design guarantees long life of consumables.
- Long Cable Length – Standard Torch cable length of 4 meters with option to extend up to 8 meters
Specifications
Technical Specifications of PTA System
Model |
PTA 200 |
PTA 400 |
Input |
Input Supply |
415VAC / 50-60Hz / 3 - Ø |
415VAC / 50-60Hz / 3 - Ø |
Max Installed Power (Hp) |
11 |
24 |
Input kVA @ 60% Duty Cycle |
9.7 |
19.4 |
Input kVA @ 100% Duty Cycle |
7.5 |
14.9 |
Output |
Open Circuit Voltage OCV (VDC) |
75 – 85 |
75 – 85 |
Current Range (A) |
5 – 200 |
5 – 400 |
Current @ 60% Duty Cycle (A) |
200 |
400 |
Current @ 100% Duty Cycle (A) |
155 |
310 |
Pilot Arc Current (A) |
10 – 25 |
10 – 25 |
Gas Parameter |
Plasma Gas Flow (LPM) |
0 – 5 |
0 – 5 |
Shielding Gas Flow (LPM) |
0 – 10 |
0 – 10 |
Carrier Gas Flow (LPM) |
0 – 15 |
0 – 15 |
Pilot Parameter |
Pilot Arc Current |
10 – 25 |
10 – 25 |
Up / Down Slope (sec) |
1 – 10 |
1 – 10 |
Pre / Post Flow (sec) |
1 – 10 |
1 – 10 |
Programmable Parameter Welding |
Gas Pre Flow (sec) |
0 – 99.9 |
0 – 99.9 |
Gas Post Flow (sec) |
0 – 99.9 |
0 – 99.9 |
Current Up Slope (sec) |
0 – 99.9 |
0 – 99.9 |
Current Up Slope (sec) |
0 – 99.9 |
0 – 99.9 |
Base Current (A) |
5 – 200 |
5 – 400 |
Manipulator |
Degree of Rotation |
0 – 360 |
0 – 360 |
Degree of Overlap |
0 – 360 |
0 – 360 |
Boom Step Over |
0 – 999 |
0 – 999 |
Number of Bands |
0 – 999 |
0 – 999 |
Rotation Speed |
|
|
Boom Travel Speed |
|
|
Moving Base |
Optional |
Optional |
Rotating Base |
Optional |
Optional |
Oscillator |
Oscillation Width (mm) |
0 – 25 |
0 – 25 |
Oscillation Per Minute |
0 – 80 |
0 – 80 |
Dwell Time Left (sec) |
0 – 99.9 |
0 – 99.9 |
Dwell Time Right (sec) |
0 – 99.9 |
0 – 99.9 |
Powder Feeder |
Hopper Volume (cc) |
700 |
700 |
Powder Feed Rate |
Auto w.r.t. current |
Auto w.r.t. current |
Feeder On / Off |
Auto with Arc |
Auto with Arc |
Feed Slope Down |
Auto w.r.t. current down slope |
Auto w.r.t. current down slope |
Water Chiller |
Flow Rate (LPM) |
5 |
5 |
Outlet Temperature (Deg C) |
10 – 30 |
10 – 30 |
Tank Capacity (Liters) |
25 / 50 / 100 |
25 / 50 / 100 |
Cooling Capacity (Ton) |
1 / 2 / 3 |
1 / 2 / 3 |
Torch |
Current Capacity (A) |
150 |
350 |
Duty Cycle (%) |
100 |
100 |
Option |
ID / OD |
ID / OD |
Number of Programs |
999 |
999 |
Hardware |
Mother Board |
Intel Dual Core |
Intel Dual Core |
Operating System |
Embedded Microsoft XP |
Embedded Microsoft XP |
Flash Drive |
|
|
PLC |
32 I / O |
32 I / O |
Additional |
Current Pre-Setting Facility |
Provided |
Provided |
High Frequency Test |
Provided |
Provided |
Water Failure Trip |
Provided |
Provided |
Gas Failure Trip |
Provided |
Provided |
Digital Ammeter & Voltmeter |
Provided |
Provided |
OCV Test |
Provided |
Provided |
Summary:
P.T.A. Deposit shows the following characteristics:
- Reduces Cost –Restoring a worn part to "as new" condition generally costs between 20-70% of a brand new replacement part
- Prolongs Equipment Life – Service life increases of 3 to 10 times are common with properly overlaid parts
- Reduces Downtime – Parts last longer and fewer shutdowns are required
- Less Spare Parts Inventory – There is no need to keep numerous spare parts when worn parts can be rebuilt
- An attractive bead with no signs of oxidation and with little or no ripple
- Very low dilution
- High, density, no porosity & no inclusions
- Micro-photos or x-rays show the deposits to be of high density & metallurgically bonded to the Substrate
Scope of supply includes:
- Inverter Power Source (Make: Lincoln Electric)
- PTA OD Torch Head 350 Amp with 4 mtr Cable
- Water Chiller cum Re-Circulator
- Powder Feeder Positive Displacement
- Digital Oscillator
- Welding Positioner
- Column & Boom
- Controller for Hardfacing System
- Consumables
Custom built computer controlled systems are available with touch screen facility with customized software as per the requirement of the jobs for Circular or Linear welds.
Circular weld can have option of Banding with step over facility typically to overlay large surface area or groove in circular form Or Spiral without step over option for screw conveyors.Linear option can be provided with only Boom travel or combination of Boom and Moving base of column & boom to give zig-zag pattern to form square or rectangular shape of deposit over large surface areas.
Plasma Transferred Arc (PTA)
& Oxy- Acetylene Process |
Plasma Transferred Arc (PTA) |
Plasma Transferred Arc (PTA) Welding |
|
|
|
|
|
|

|