Tig Welding
Tungsten inert gas (TIG) welding became an overnight success in the 1940s for joining
magnesium and aluminium. Using an inert gas shield instead of a slag to protect the weldpool,the process was a highly attractive replacement for gas and manual metal are welding. TIG has played a major role in the acceptance of aluminium for high quality welding and structural applications. The process may employ direct current with positive or negative electrode or alternating current. In general, ac is preferred for welding aluminum and magnesium. Direct current electrode negative is preferred for welding most other materials and for automatic welding of thick aluminum. Thin magnesium sometimes is welded with direct current electrode positive. When ac is used with argon shielding, an arc cleaning action is produced at the joint surfaces on aluminum and magnesium. This cleaning action removes oxides and is particularly beneficial in reducing weld porosity when welding aluminum. When using dc, helium may be used as the shielding gas to produce deeper penetration. However, stringent precleaning of aluminum and magnesium parts is required with helium shielding. Argon and helium mixtures for gas shielding can provide some of the benefits of both gases.
Regardless of polarity, a constant current (essentially vertical volt-ampere characteristic) welding power source is required. In addition, a high-frequency oscillator is generally incorporated in power sources designed for GTAW. High-frequency can be employed with dc to initiate the arc instead of touch starting to minimize tungsten electrode contamination. Normally, the high frequency is turned off automatically after arc ignition. The high frequency power is normally operated continuously with ac to maintain ionization of the arc path as the arc voltage passes through zero.
Some special power sources provide pulsating direct current with variable frequency. This provision permits better control of the molten weld pool when welding thin sections, as well as when welding in positions other than flat. Pulse repetition rates are adjustable as are the pulse profiles. Other pulse features are also controlled. Power supplies may include electronically controlled features such as "up slopes" and "down slopes", etc. The latter are necessary to eliminate craters and crater cracking at the beginning and ends of welds or to accommodate thickness changes, etc. For manual welding much of this power supply sophistication is not used, as the skilled welder modifies his technique as he observes variations in the weld pool during the progress of the weld.
Melting followed by fusion of the weld joint results from the flow of electrons, (the arc current) and the very high temperature of the arc plasma through which the current passes and which provides the conductance path. The arc comprises both the current and plasma, along with some generated metallic vapors, etc. Plasma temperature at the electrode can be tens of thousands of degrees Fahrenheit depending on amperage. Within the arc region it can be ten to twenty thousand degrees Fahrenheit. Considerable heat is lost by radiation and in this regard arc efficiency drops.Depending on circuit polarity, the arc may emanate from the tungsten electrode or from the workpiece. Most often direct current is used but alternating current is advantageous for welding materials which form refractory oxides, for example aluminum. Due to the complex physics of the arc, involving electron collisions, pressures, temperature gradients, etc. the arc forms what is sometimes referred to as an "umbrella" shape. Because of this, arc length must be very short if narrow welds are to be achieved. Welder skill is therefore challenged to avoid tungsten inclusions in the weld pool and electrode contamination. Since the arc and plasma is not focusable the concentration of energy in the arc cannot equal with that developed in the electron and laser beam processes and therefore, GTAW welds due to the lower rate of energy input are usually wider and have wider heat affected zones. As a result GTAW welds are more prone to distortion, wider heat affected zones and stresses.
We must emphasize this is not intended to imply that GTAW welds are lower quality, they are in fact of excellent quality. GTAW welding can be called the workhorse of industrial production welding. The low cost of the equipment and its versatility along with excellent weld quality are the basis of its popularity. In addition, and due to the slower cooling rate GTAW welds may contain less porosity, lack of fusion or the formation of brittle martensite than can result from the concentrated energy beams of either the laser or electron beam processes which are both characterized by very rapid cooling and weld solidification. Rapid cooling is associated with martensite formation - a brittle phase which has the potential for cracking.
As in other welding processes there are subtleties. Arc instability, arc blow and wander all seriously affecting the operation and weld quality can result from magnetic influences, improper electrode preparation, poor maintenance, improper electrode size, incorrect arc voltage, base metal surface oxidation, inadequate shielding gas flow rates, coverage and purity. Welds in restricted channel like areas can also reflect the results of arc instability. Shielding gas contaminated with moisture or oxygen, resulting from hose leaks or moisture on interior hose surfaces have their destructive effects on weld quality. Efficiency of shielding gas coverage is important to avoid weld pool and electrode contamination. Physically and chemically dirty joint surfaces inhibit the "wetting" action of the molten weld pool causing lack of fusion, along with porosity and inclusions.
Gas tungsten arc welding is a thermal process depending on conducted heat through the weld joint materials to achieve penetration. In this respect its conductance mode is similar to laser and electron beam. They differ substantially, however, in the thermal impingement area dimension and their rates of energy input. The impingement areas of the laser and electron beams may be .010" or .020" in diameter whereas the gas tungsten arc impinges on an area many times that and, in addition and unlike laser and electron beam is supplemented by the high temperature radiation and thermal convection of the plasma which result in additional heating of the areas adjacent to the weld. GTAW penetration is limited to materials less than .250" thick. Beyond this the weld joint must be prepared by beveling the joint edges forming a "V" or "U" shaped joint geometry when the workpiece details are butted. Beveling the weld joint by material removal eliminates the need to conduct the arc heat from the joint surface through to the root. In effect, a crucible is configured and filled by filler wire addition in the welding operation. Therefore, deeper penetration is dependent not so much on thermal conductance but by the deposition of filler wire to fill the groove. Welder skill is required. The resultant unbalanced fusion weld geometry, wide at the top and narrow at the bottom can produce significant distortion. Restraining fixtures are most often used to reduce this problem. If restraining fixtures or clamps are used contractual stress generation develops. Depending on the materials and level of stress immediate or delayed cracking can result.
Several types of tungsten electrodes are used with this process. Thoriated and zirconiated electrodes have better electron emission characteristics than pure tungsten, making them more suitable for dc operations. The electrode is normally ground to a point or truncated cone configuration to minimize arc wander. Pure tungsten has poorer electron emission characteristics but provides better current balance with ac welding. This is advantageous when welding aluminum and magnesium.
Affect of electrode tip on penetration profile.
Sharper Electrodes |
Blunter Electrodes |
Easy arc starting |
Usually harder to start the arc |
Handle less amperage |
Handle more amperage |
Wider arc shape |
Narrower arc shape |
Good arc stability |
Potential for more arc wander |
Less weld penetration |
Better weld penetration |
Shorter electrode life |
Longer electrode life |
Electrode taper
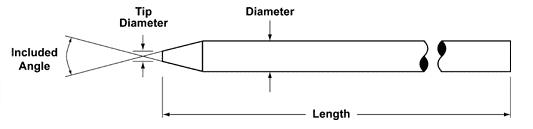
Electrode Taper - This is usually called out in degrees of included angle (usually anywhere between 14 degrees and 60 degrees). Below is a summary chart that illustrates how different tapers offer different arc shapes and features:
The equipment needed consists of a welding torch, a welding power source, a source of inert gas with suitable pressure regulators and flowmeters, a welding face shield, and protective clothing. Electric power requirements depend upon the type of material and the thicknesses to be welded.
|